Hydrogen
Tailored solutions for regulating mass flow and pressure have the potential to overcome obstacles within the hydrogen industry. From direct regulation of electrolysis and fuel cell system processes, to test benches for membrane and catalyst verification, Alicat offers countless flow and pressure solutions so you can focus on creating a more sustainable future.
Applications
Electrolysers
Back pressure controllers with custom-sized valves and anti-corrosive build options ensure stability even in high humidity and temperature environments. Mass flow meters, equipped with totalizers, provide accurate monitoring of H2 and O2 flows. Coriolis mass flow technology guarantees precision measurement and control of DI water in low-flow rate scenarios.
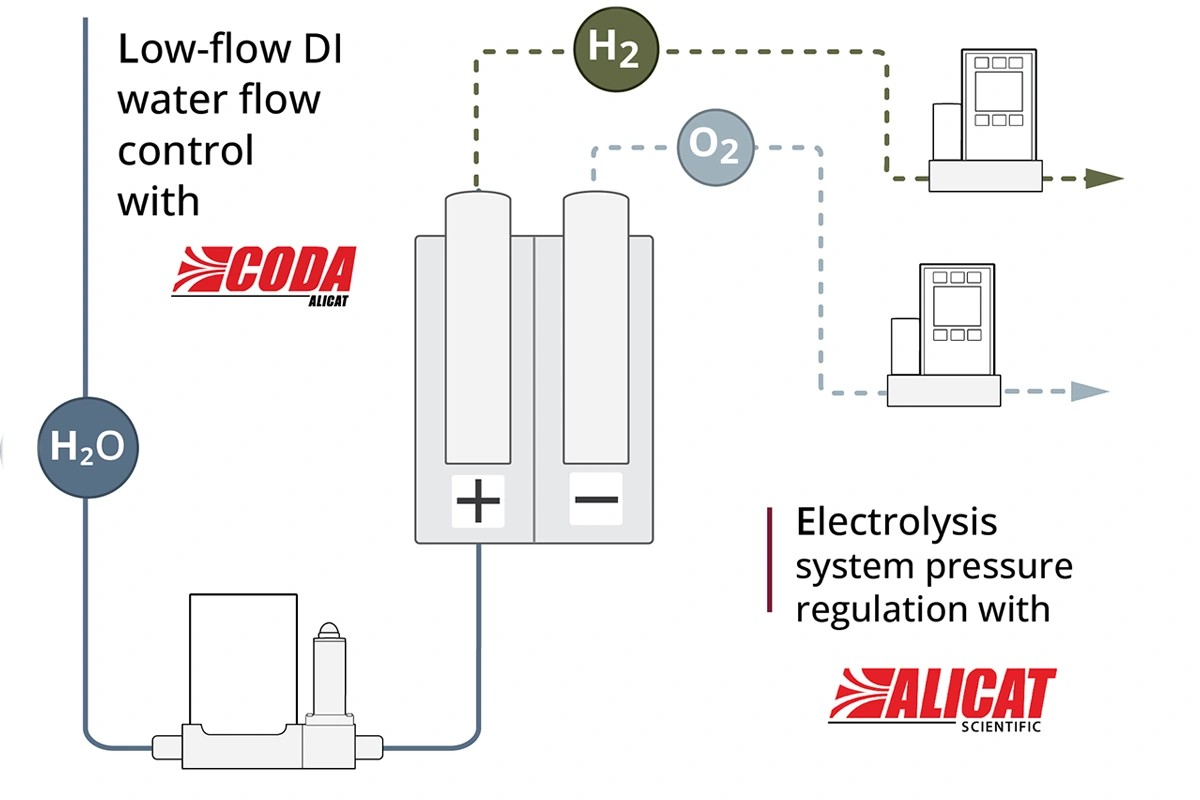
Fuel Cells
Tailored solutions for precise regulation in fuel cell systems supports manufacturers in optimizing efficiency during testing and production. Alicat controllers, known for accuracy and scalability, address challenges across processes. Processes extends from leak checks and membrane permeability tests to the overall regulation of fuel cell systems, ensuring reliable performance and system integrity throughout the design and manufacturing process.
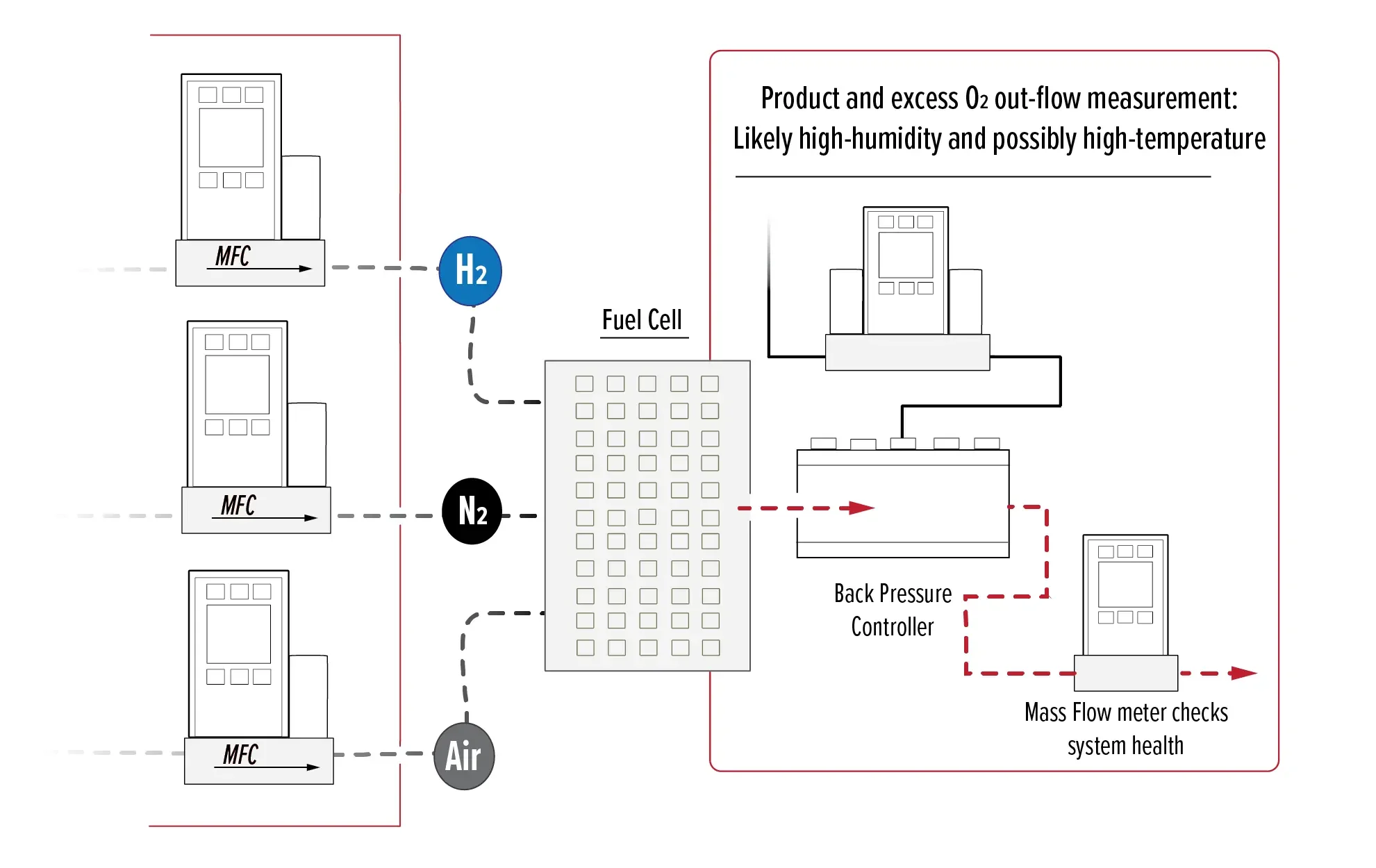
Novel Processes
From CO2 hydrogenation to electrolyser verification, to pressure swing absorption systems, companies trust Alicat to provide customized support and products that help scale and improve their hydrogen processes.
Read how Alicat’s precise pressure control improved stability for a hydrogen analysis system
Products
CODA Coriolis mass flow controllers precisely control DI water or high pressure gases.
Hydrogen mass flow meters with integrated totalizers make monitoring easy, up to 12,000 SLPM.
Hydrogen mass flow controllers mimic fuel cell behaviors at full scale flow rates up to 12,000 SLPM with quick response and high accuracy.
Dual-valve pressure controllers reach setpoints in milliseconds and maintain control without continuous bleeding.