Glass and Optical Fiber
Accurate, repeatable production of high-purity glass optimizes optical fiber production and maximizes transmission, accelerating the transition to 5G.
Fabricate high-purity preforms and draw low-loss glass and optical fiber
Use mass flow to regulate the flow of inert, shielding, and dopant gases with greater control than standalone valves.
- Automatic adjustment to ambient atmospheric conditions. Prevent batch losses in outdoor draw towers with valves that respond quickly to changes in weather or barometric pressure.
- Full batch-to-batch repeatability. Highly repeatable flow of fuel and shielding gases guarantees final product consistency.
- Lowest lifetime cost of ownership. Industrial communication provides preventative maintenance metrics, while compatibility with a wide range of flows and gases minimizes the need for spares.
Applications
Tightly controlling fuel and shielding gases maintains preform purity
Prevent impurities during preform manufacture and polish steps using tight flow control of dopant and inert gases.
Minimize system fluctuations and guarantee smooth ribbon coatings with highly accurate pressure control.
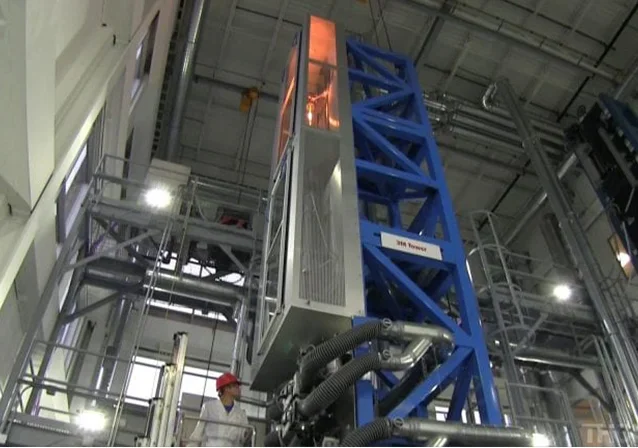
Maximizing transmission to build the 5G network
Introduce new process lines without affecting supply pressure of existing lines and increase transmission using fast, high precision devices with easy automation.
Products
Products
CODA Coriolis mass flow controllers precisely control DI water or high pressure gases.
Hydrogen mass flow meters with integrated totalizers make monitoring easy, up to 12,000 SLPM.
Hydrogen mass flow controllers mimic fuel cell behaviors at full scale flow rates up to 12,000 SLPM with quick response and high accuracy.
Dual-valve pressure controllers reach setpoints in milliseconds and maintain control without continuous bleeding.