Graftel Verifies Sensor Operation in Nuclear Leak Monitoring Equipment
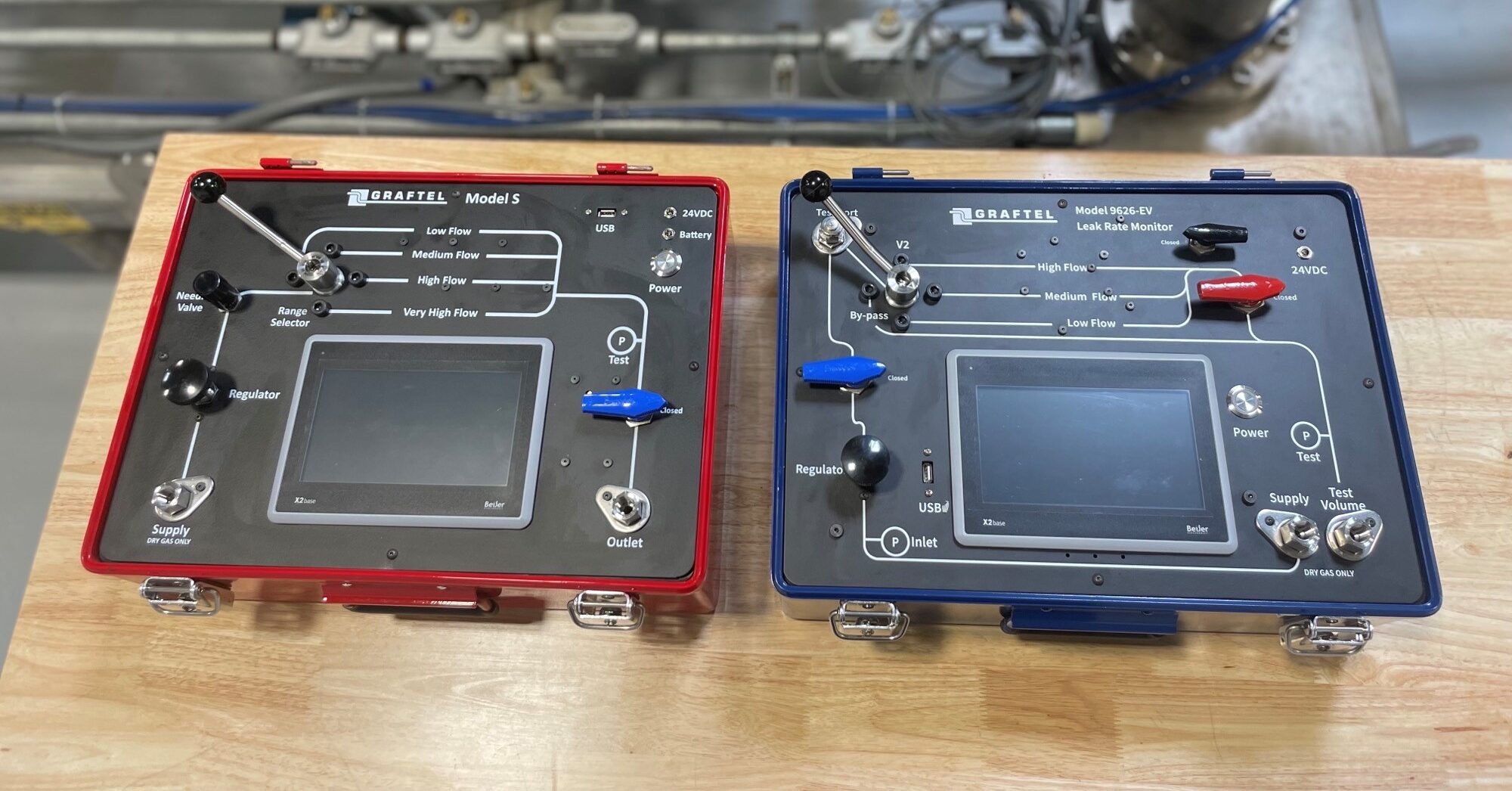
Founded in 1991 and headquartered in Roselle, Illinois, Graftel has emerged as the industry leader for nuclear facility leakage rate monitoring in the US. Regular monitoring both satisfies federal NRC regulations and serves as a preventative measure to help keep the working environment safe for power plant employees. From portable local leakage rate tests (LLRTs) to building‑scale integrated leakage rate tests (ILRTs), Graftel is the preferred partner in testing for leakages at more than 90% of America’s nuclear power plants, as well as many others around the world.
Integrated leak rate test verification
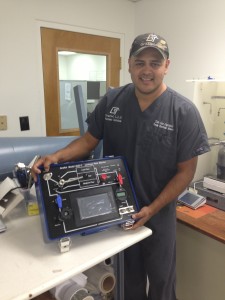
The Nuclear Regulatory Commission (NRC) requires that all nuclear power plants undergo regular testing to ensure they comply with containment leakage requirements according to NRC 10 CFR 50 Appendix J. The requirements include three types of testing:
- Type A tests measure the overall integrated leakage rate for the primary reactor containment.
- Type B tests measure local leakage for primary reactor containment penetrations, including airlocks and electrical penetrations.
- Type C tests measure containment isolation valve leakage rates.
Graftel invented their smart sensor technology for Type A ILRTs in 1993. Since then, Graftel’s ILRT has become the primary system used in the US. Smart sensors have made ILRTs more efficient by reducing both the time and the number of penetrations required to set up and conduct the tests. Not only does Graftel design and manufacture the smart sensors used in the ILRT, but they also calibrate them. After years of experience in calibrating their own instruments, Graftel established a top‑notch calibration laboratory that is ISO 17025 certified and now services flow, pressure, temperature, and humidity instrumentation.
During an ILRT, Graftel engineers pressurize the reactor building to 46 PSIG for a period of 8 hours. More than 50 Graftel smart sensors mounted inside the reactor return continuous temperature and humidity data to calculate pressure decay throughout the testing period.
Following the conclusion of the primary test, the Graftel team performs a verification test. Using pressure taps in the building, the team induces a steady leak of about 50 SLPM. During this test, Alicat mass flow meters monitor the actual leakage rate as the smart sensors continue to report their data.
The two data sets are compared to verify that the smart sensors are operating within the required accuracy specifications. Graftel relies upon Alicat mass flow meters for their measurement accuracy and insensitivity to changes in pressure and temperature during the 5‑hour verification test.
Local leakage rate test (LLRT) monitors
Sometimes, the most devastating failures are caused by the smallest of components: valves, flanges, or electrical penetrations. Having secured their position in Type A testing, Graftel began to design a portable leakage rate monitor that would be suitable for Type B and C testing in nuclear facilities. Today, Graftel’s local leakage rate test (LLRT) monitor (Model 9623) is a rugged, high‑precision device capable of performing B and C testing via either flow make‑up or pressure decay methods.
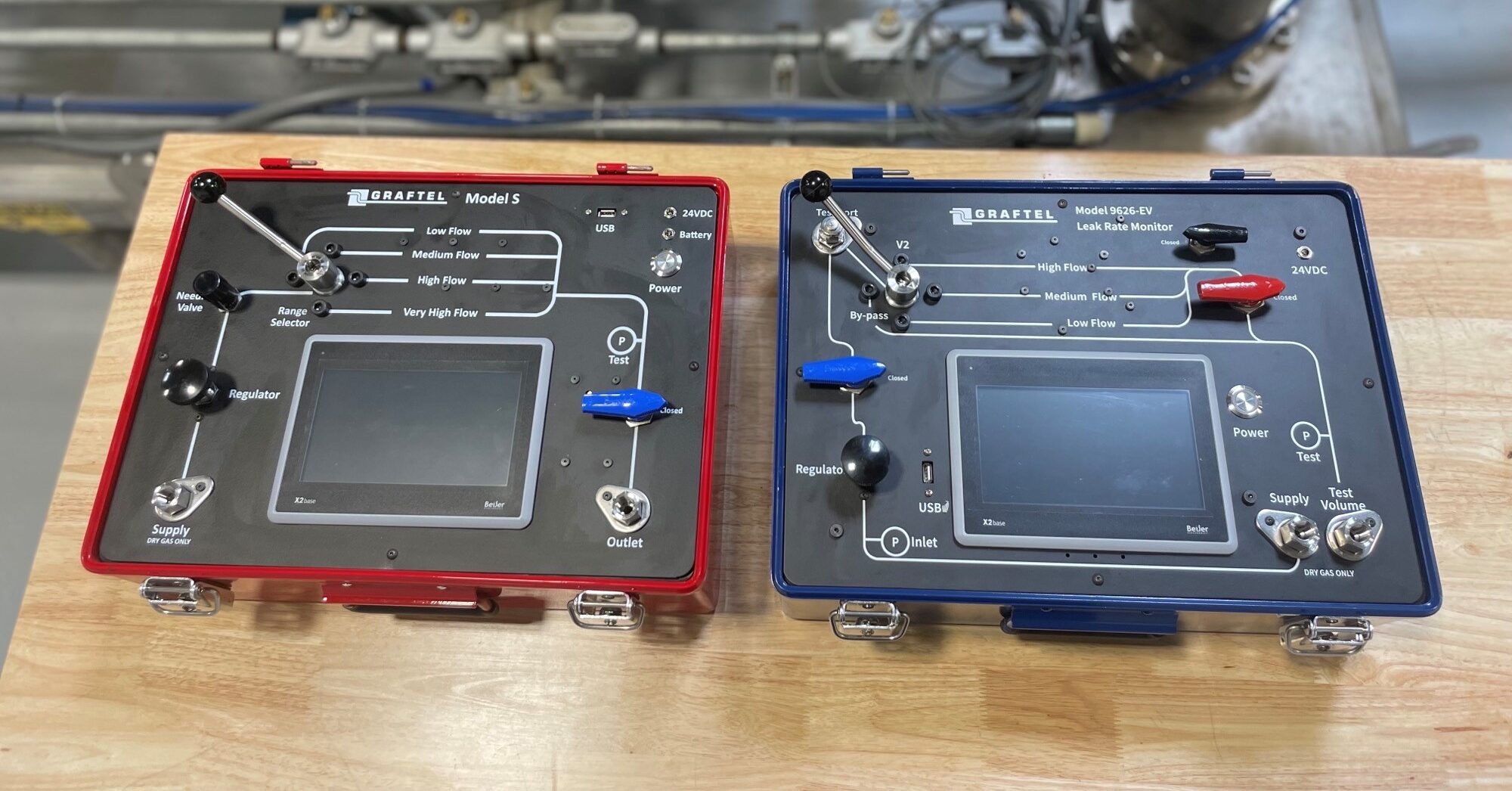
In a typical Type B test on a containment airlock, the airlock is sealed and pressurized to 50 PSIG. Air or nitrogen is supplied to the LLRT pressure regulator, which maintains the designated test pressure within the airlock. If the regulator allows additional flow into the airlock to maintain the test pressure, then this is evidence that leaks are present. The flow rate into the airlock reveals the degree of leakage out of the airlock. Every LLRT incorporates three Alicat mass flow meters to monitor high, medium, and low flow ranges, depending upon the needs of the particular test.
Whereas an airlock Type B test may require a high or medium range, a Type C test on an isolation valve may require the lowest flow range. Custom flow ranges may be ordered from Graftel as individual nuclear plant needs require them. Graftel also offers an LLRT version (9623 Model S) that serves as a leakage rate monitoring standard with four Alicat mass flow meters inside.
As OEM components for the LLRT, Alicat’s mass flow meters were an easy choice for Graftel. Alicat’s RS‑232 communications protocol is standard on every mass flow meter and supports multi‑drop natively. This allows easy integration of three Alicats with a single user interface designed by Graftel. The LLRT touch screen and Graftel programming allows users to directly access meter functions such as tare and gas select from a central interface. Since the LLRT is intended to be a rugged, portable unit, the mass flow meters inside it must also satisfy these conditions. With no moving parts or power‑consuming heating elements, Alicat mass flow meters are energy‑efficient and insensitive to bumps, vibrations, or changes in orientation.
Some of Graftel’s earliest LLRTs have returned for maintenance still holding their original calibration accuracy after 11 years of use in the field. When radioactive contamination or other local plant conditions make annual recalibrations at the factory impossible, nuclear power plant engineers need to know they can still trust their leakage rate monitors. Together, Graftel and Alicat make that possible.