Welding Shield Gas Mixing at the Canadian Centre for Welding and Joining - University of Alberta
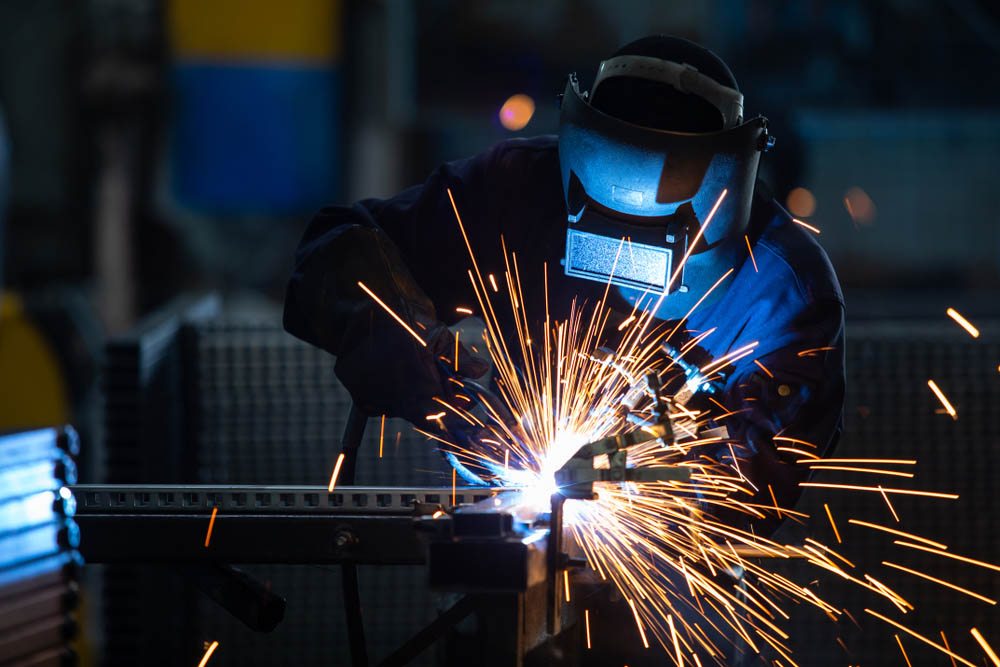
Precision in shield gas mixing can optimize weld quality, efficiency, and safety. Understanding the impact of shield gas composition as it relates to weld characteristics can lead to innovations that reduce fume emissions, improve deposition rates, and enhance automation. The Canadian Centre for Welding and Joining (CCWJ) at the University of Alberta is at the forefront of this research, leveraging advanced gas mixing technologies to push the boundaries of welding science.
Using Alicat® Scientific’s FusionFlow™ IMX Industrial Gas Mixer, the CCWJ was able to significantly streamline their gas storage systems and create precise gas blends on demand. Opening new avenues for industrial and scientific applications.
The University of Alberta’s research team, in collaboration with Alicat, is transforming welding through innovative shield gas blending techniques, paving the way for safer, more cost‑effective, and environmentally friendly welding processes.
The Canadian Centre for Welding and Joining (CCWJ) at the University of Alberta (UofA) is a world‑class research and engineering training center which was established in 2010 to address the needs of resource‑based industries in Canada. Our research activities focus on everything from fundamentals to applied research, and cover virtually all welding and joining processes in a broad range of material systems. Being located right at the epicenter of manufacturing for oil and gas operations, the CCWJ interacts daily with the whole supply chain of manufacturing and fabrication, from end users to manufacturers, to suppliers of consumables. Generous donations from industry and government grants have provided more than $3 million in equipment for the Centre’s four labs, which also includes Alicat’s FusionFlow™ IMX Industrial Gas Mixer for making custom blends of gases; up to 4 at a time.
FusionFlow uses Alicat Mass Flow Controllers (MFCs) exclusively. In 2016, these MFCs allowed us to move away from individual cylinders to a centralized gas delivery system with pure gases only. The pure gases are blended for each machine and setup based on the application requirements. This not only helped us improve our scientific capabilities, but it also helped us significantly reduce the footprint of a stock of approximately 40 cylinders at any given time to only 15. Now the bulk of our stocked welding gases consist of pure Argon (Ar) and Carbon Dioxide (CO2), to which we add specialty gases and mix an optimized blend for each application on the fly with high precision. The rest comprises some specialized high‑gases for high‑sensitivity analyzers. This has freed up urgently needed space to set up equipment and experiments, and has also immensely simplified our gas needs and resulted in noticeable cost savings.
With these capabilities we have undertaken a series of studies on the effect of shielding gases in various welding applications using Gas Metal Arc Welding (GMAW). The GMAW process is of great industrial importance due to high efficiency of the process and its use with wide range of ferrous and non-ferrous alloys. Shielding gases play a core role in this process, as they protect the molten weld pool, but also affect the metal transfer [1].
Careful selection of the shielding gases optimizes the efficiency of the process and can have significant effects on the appearance of the weld; penetration, sidewall fusion, and weld toe contour; wetting of additive elements (e.g. metal core, tungsten carbides); arc start and stability; and formation and retention of oxides.
Gases commonly used for the process include pure Ar and CO2, some binary blends in varying percentages (e.g. Ar + CO2, Ar + Oxygen, Ar + Helium, Ar + Hydrogen), as well as ternary gas blends. This depends on the type of metal used as well as other factors such as weld position, and small variations in percentages will have a noticeable impact on appearance, deposition efficiency, and weld performance.
Our research on the underlying fundamentals looked in particular at the temperature of droplets in various metal transfer modes and materials, as well as the fall voltages that affect the heating of droplets, anode and cathode. Of special interest to us was the transition zone between globular and spray transfer, which we studied using a calorimeter setup in conjunction with the FusionFlow Gas Mixer. Beyond their scientific contribution, these studies have industrial importance, since they explored the ability to reduce welding fume emissions. The experiments showed that by using welding parameters and shielding gas composition to target the transition zone, the droplet temperature can be lowered, thereby reducing the fume generation, while maintaining a similar deposition rate [2].
The shielding gas composition shifts the droplet temperature curve to higher currents but do not appear to significantly shift the curve to different temperatures. When studying fall voltages and advanced waveforms for Aluminum wires, the findings also highlighted a strong impact of shielding gas composition, and further studies will be undertaken to explain the interaction fundamentally [3].
These studies provided strong indication that a careful selection of welding parameters and shielding gases can reduce the fume emission using existing materials while retaining their material properties and deposition rates. The use of gas blending thereby provides another avenue to explore to meet new occupational exposure limits (OEL) of elements such as Manganese with the potential to reduce the amount of PPE or filtration necessary.
The ability to use the FusionFlow Gas Mixing system with pure gases and adjust the blends “on the fly” for each application introduces cost‑on the gas side and optimizes weld economics by improving:
- Weld safety
- Quality
- Efficiency
- Significantly enhance welding automation setups, in which gas blends can be adjusted to account for changes in weld position within a program
- Respond to feedback loops to optimize deposition
In addition to the above mentioned points, a nice side effect is also the built‑in pressure management capabilities that can provide central monitoring for QA purposes, reduce welding flaws by stabilizing flow rates and providing feedback of pressure loss in the system, and simplify purchasing by indicating when supply needs to be replenished.
Citations
- [1] J. Nadzam, F. Armao, L. Byall, D. Kotecki, and D. Miller, “Gas Metal Arc Welding Product and Procedure Selection,” C4.200, p. 96, 2014.
- [2] C. McIntosh, J. Chapuis, and P. Mendez, “Effect of Ar‑CO2 Gas Blends on Droplet Temperature in GMAW,” Weld. J., vol. 95, no. 8, pp. 273s – 279s, 2016.
- [3] C. McIntosh and P. F. Mendez, “Fall voltages in advanced waveform aluminum GMAW,” Weld. J., vol. 96, no. 9, pp. 354s – 366s, 2017.
Authors
- Patricio Mendez is a Professor in Chemical and Materials Engineering at the University of Alberta.
- Goetz Dapp is Associate Director of the CCWJ.