Alicat Mass Flow Controller for Polyurethane Slabstock Processes
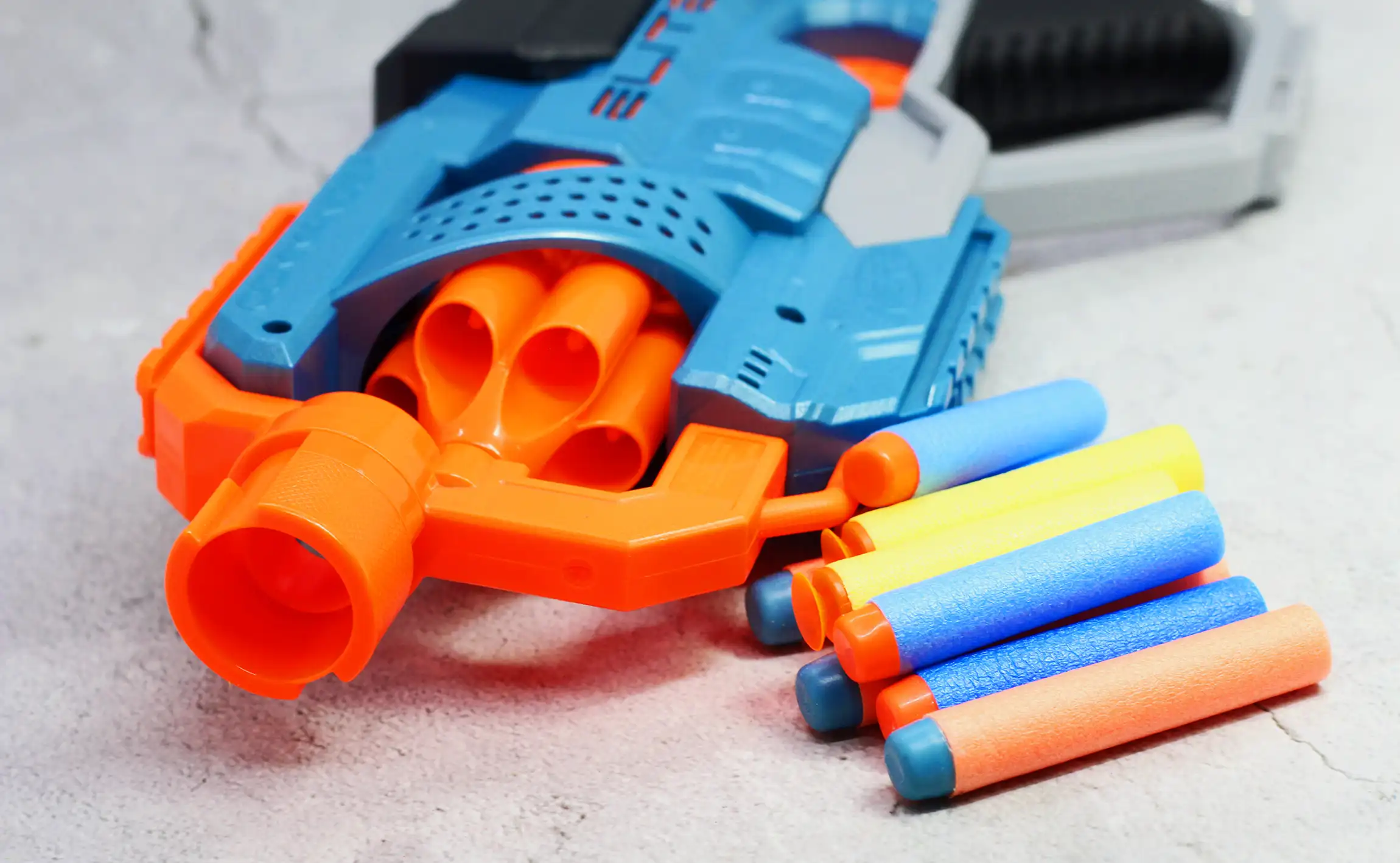
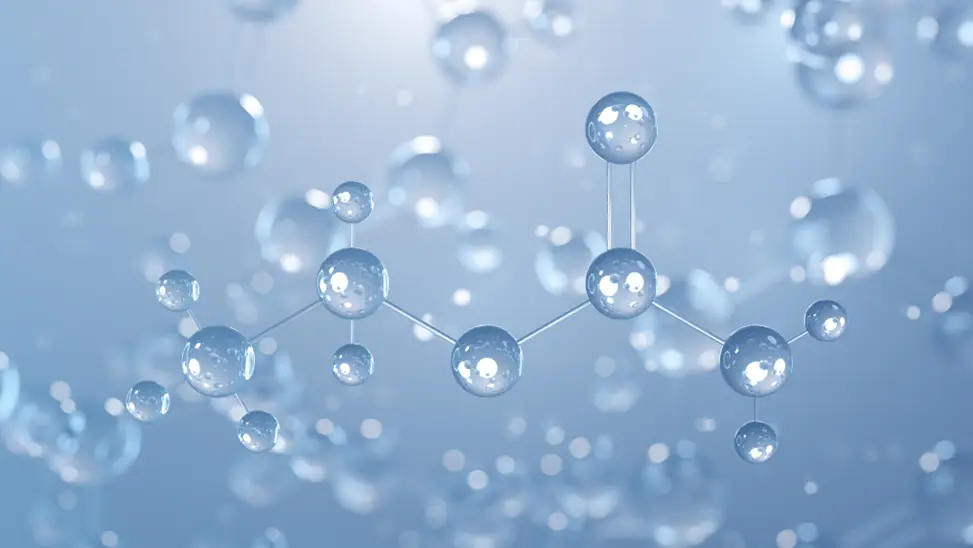
How is polyurethane foam produced?
PU can be created through different methods, but in general, it is made by mixing polyols (an organic molecule containing one or more hydroxyl (OH) groups), isocyanate compounds (compounds containing the isocyanate (NCO) groups) and blowing agents.
Blowing agents are categorized as chemical (e.g., water reacting with isocyanates to produce CO₂) or physical volatile liquids that vaporize during the reaction.
Other additives like surfactants, catalysts, dyes, and cross-linkers are mixed in to create a bright neon chemical slurry primed and ready for foaming.
In slab stock production, these ingredients are mixed with air inside of a single-shot system before being blasted onto a conveyor belt. As the name suggests, the foam that rises from the liquid expands to fill the conveyor and results in a massive, continuous slab of foam.
This slab is then guided down the track with wax paper and cut into smaller pieces for additional curing.
But what about the bubbles
The chemical reaction which gives PU its porous cellular structure is made up of a two-stage process of polymerization and gas generation.
Polymerization begins a chain reaction, forming urethane linkages between other polyols and isocyanates. Simultaneously a physical agent, like water, is blown into the diisocyanates creating CO₂. The CO₂ gas then becomes trapped, creating microscopic gaps inside of the foam.
As it reacts with water, billions of gas bubbles ranging from several centimeters to less than 50 microns (µm) –approximately the width of a hair- in size are uniformly distributed throughout the foam. Its density lies somewhere between 0.25 to 0.65 g/cm³ depending on the manufacturer’s formula.
Polyurethane foam often contains a larger amount of open cell bubbles, which results in a much softer, squishier product- think couch cushions and microphone pop filters. The cell count affects density, load-bearing capacity, and structure. Foam can contain a different percentage of closed vs open cells, resulting in different structural properties
The structural characteristics of two-component flexible polyurethane foam can be precisely controlled via the air pressure applied during the foaming and curing process. This influences the percentage of closed cells, alters the density, and ultimately affects the foam’s overall performance as well.
Slab stock production is a common method of yielding large amounts of soft, open cell foam but has the capability to create more rigid types of foam depending on the manufacturer’s preference.
Mass flow in foam production
Foam production involves a series of complex chemical reactions which can be destabilized by very minute changes. Deviations in raw materials, rate of mixing, humidity and formula can have disastrous effects on the form and morphology of the foam.
These non-replicable defects present a threat to large batches that rely on continuous pouring; as such, polyurethane foam slab stock production calls for a high level of repeated precision and measurement.
For customers in this industry, Alicat Scientific’s low flow laminar dp mass flow controllers presented itself as a solution.
Controllers rated for 50 SCCM gas flow at 100PSIG were used to regulate air within mixing chambers designed to combine chemicals in their gaseous state.
Some of the foam’s precursors would crystallize in the presence of water, which called for the ability to monitor the humidity of compressed air and gases at any given moment.
As a result, the Alicat mass flow controllers they ordered were equipped with relative humidity sensors and displays to monitor and maintain stability throughout the process.
By regulating flow in the mixing chamber with Alicat levels of precision, the foam dimensions and other variables that controlled desirable physical properties became easy to control in real time.
Other potential uses
During the foam’s chemical expansion, endothermic reactions can cause a system’s temperature to rise. If unchecked, this can lead to combustion or scorching of product.
The installation of air flow control systems for temperature regulation had been seen previously in glass production industries. Alicat high flow MFCs were used to maintain cooling gas flows for plate glass at a precise rate.
A different situation called for an Alicat CODA Coriolis pump to transport liquid precursors in a vacuum setting. A similar use is present in the single-shot systems for slab stock production.
With response times as low as 30 ms, and steady state control ranges of 0.1 – 100% of full scale, Alicat pressure controllers mean users can maintain and change pressures for pre and post curing treatment, for accurate control of the density and cell size of their foam.
Why it matters
When considering the finer details of any industry, it’s easy to forget the wealth of expertise used to manufacture these products. The science that has turned foam production into one of the largest global industries is—more often than not—trivial to the end users of a product. They don’t see how it’s made, ergo, it’s not that important.
Perhaps there’s a case to be made that not everyone has to know about the chemical expansion of foam slabs, but what is important is just how dependent people are on polyurethane foam. Humanity has harnessed the power of thermosetting polymers and condensed them into comfortable furniture, soft mattresses, and house insulation.
As an aide to sustainability, around 30% of polymers found in rigid polyurethane foam can find second life applications in construction materials after being ground and recycled.
So next time you’re resting on your couch or lining your Nerf gun up to your target, be sure to thank your foam for supporting everything you do.